Coca-Cola Product Recall: European Market
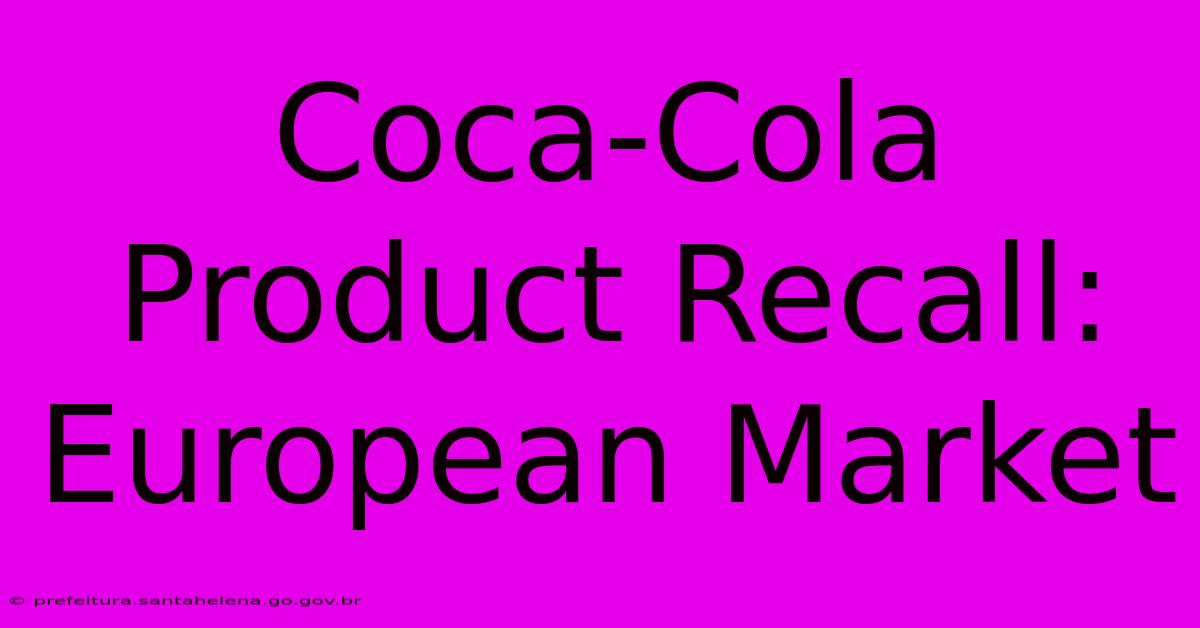
Discover more detailed and exciting information on our website. Click the link below to start your adventure: Visit Best Website. Don't miss out!
Table of Contents
Coca-Cola Product Recall: A Deep Dive into the European Market
Coca-Cola, a global beverage giant, enjoys immense popularity worldwide. However, even the most established brands are not immune to product recalls. While Coca-Cola hasn't experienced widespread, large-scale recalls in the European market comparable to some other food and beverage companies, several instances have highlighted the importance of stringent quality control and consumer safety. Understanding these events and their impact is crucial for both the company and consumers. This article delves into the history of Coca-Cola product recalls in Europe, analyzing the causes, responses, and long-term consequences.
Understanding the Scope of a Product Recall in the European Union
Before examining specific Coca-Cola recall events, it's vital to understand the regulatory landscape in the European Union. The EU has a robust food safety system, with regulations like Regulation (EC) No 178/2002 laying the foundation for food safety and traceability. This framework necessitates stringent quality checks throughout the production, distribution, and sale processes. A product recall, initiated either voluntarily by the company or mandatorily by authorities, involves removing a product from the market due to safety concerns. These concerns can range from contamination (bacterial, chemical, or physical) to inaccurate labeling or misleading advertising, impacting consumer health and trust. The scale of a recallβfrom a limited regional withdrawal to a widespread pan-European actionβdepends on the severity and scope of the problem.
Examining Past Incidents: A Case-by-Case Analysis
While large-scale, headline-grabbing recalls involving Coca-Cola products are rare in Europe, smaller incidents and localized withdrawals have occurred. These often involve issues at specific bottling plants or distribution centers rather than widespread manufacturing defects. Unfortunately, detailed public information on these smaller scale recalls is often limited. Companies frequently address issues internally to avoid damaging their brand reputation. However, even these smaller events underscore the importance of proactive quality control measures.
One example that highlights the vigilance required is the potential for glass fragments in bottles. While not a specific recall attributed directly to Coca-Cola's manufacturing process, incidents involving glass contamination in beverages have occurred across different brands in the EU. This emphasizes the importance of rigorous quality checks at every stage of the supply chain, from the manufacturing of glass bottles to the filling and distribution of the product. Such incidents, though not directly attributed to Coca-Cola, serve as cautionary tales illustrating the potential risks and the need for robust preventative measures within the industry.
Another area that requires consistent monitoring is labeling accuracy. EU regulations strictly govern the labeling of food and beverages, including ingredients, nutritional information, and allergen declarations. Any discrepancy in labeling can lead to a recall, particularly if it involves allergens like nuts or dairy that can trigger severe reactions in sensitive individuals. Coca-Cola, like all food and beverage companies, must maintain meticulous records and adhere strictly to labeling regulations across its diverse European product lines.
The Role of Transparency and Consumer Trust
The aftermath of any product recall, regardless of its scale, is critical for maintaining consumer trust. Transparency in communicating with consumers and regulatory bodies is paramount. A swift and decisive response, including clear communication about the problem, the affected products, and the remedial action taken, is vital in minimizing damage to the brand's reputation. Open communication reassures consumers that their safety is prioritized and helps build confidence in the company's commitment to quality.
Coca-Cola's history, while generally devoid of major European recalls, underscores the importance of maintaining a proactive approach to quality control and consumer safety. Their robust internal quality management systems likely play a crucial role in preventing larger-scale issues. However, even with the best preventative measures, unforeseen events can occur. The ability to effectively manage and communicate such events is crucial for maintaining consumer trust and brand loyalty.
The Impact of Supply Chain Management
The vast and complex supply chain involved in distributing Coca-Cola products across Europe presents unique challenges. Maintaining consistent quality control across numerous bottling plants, distribution centers, and retail outlets requires sophisticated monitoring systems and stringent quality control checks at every stage. Any breakdown in the supply chain, however minor, can potentially lead to product contamination or distribution errors, underscoring the need for robust traceability systems.
Effective traceability allows for quick identification and isolation of affected batches, limiting the scope of any potential recall. This also highlights the importance of collaboration with suppliers, distributors, and retailers in ensuring consistent product quality and rapid response times in the event of a problem. Open communication channels and shared responsibility for product safety are essential components of a well-functioning supply chain.
Future Considerations and Best Practices
While major Coca-Cola product recalls remain infrequent in Europe, the company must continually refine its quality control measures and supply chain management to maintain its high standards. Investing in advanced technologies for monitoring and traceability, strengthening communication channels across the supply chain, and maintaining open communication with consumers remain crucial aspects of mitigating future risks.
Furthermore, continuous monitoring of regulatory changes and best practices within the food and beverage industry is essential. Staying ahead of potential issues through proactive risk assessments and regular audits can significantly reduce the likelihood of future recalls. The European food safety regulatory landscape is constantly evolving, demanding ongoing vigilance and adaptation from companies like Coca-Cola.
Conclusion: A Proactive Approach to Safety
Although significant Coca-Cola product recalls have been relatively rare in the European market, the potential for issues remains. The company's commitment to consumer safety is best demonstrated not by the absence of recalls, but by its proactive approach to quality control, transparent communication, and robust supply chain management. Maintaining these high standards is crucial for preserving consumer trust and ensuring the long-term success of Coca-Cola's European operations. The focus should remain on preventative measures, continuous improvement, and a culture of safety that prioritizes consumer well-being above all else.
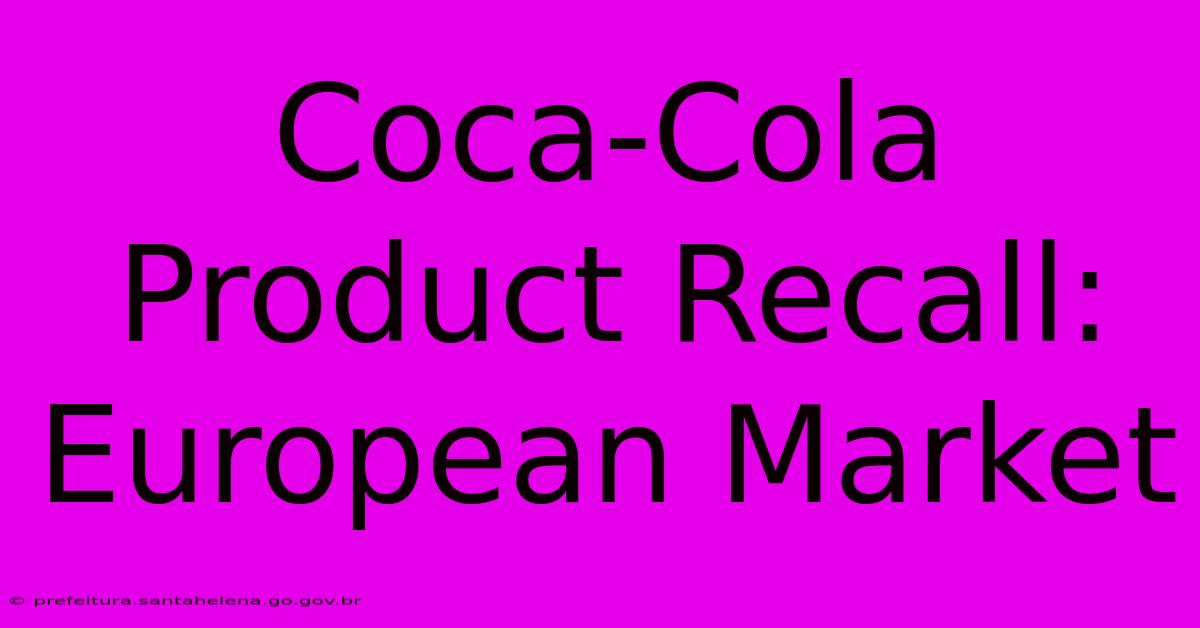
Thank you for visiting our website wich cover about Coca-Cola Product Recall: European Market. We hope the information provided has been useful to you. Feel free to contact us if you have any questions or need further assistance. See you next time and dont miss to bookmark.
Also read the following articles
Article Title | Date |
---|---|
Nvidia Aktie Ueberbewertet Oder Zu Unrecht Abgestraft | Jan 28, 2025 |
David Coote Former Referee Comes Out | Jan 28, 2025 |
Neymars Emotional Al Hilal Farewell | Jan 28, 2025 |
Popular Burger Chain Almost Famous Closes Shops | Jan 28, 2025 |
Selena Gomez Counters Politicians Statement | Jan 28, 2025 |
Bucks Beat Jazz 125 110 Jan 28 2025 | Jan 28, 2025 |
Gomez Addresses Political Controversy | Jan 28, 2025 |
Bucks Beat Jazz In Close Contest | Jan 28, 2025 |
Homans Comments On Gomez Crying | Jan 28, 2025 |
Nasif Confirma Banfield Fue Buena Opcion Espn | Jan 28, 2025 |