Coca-Cola Product Recall In Europe
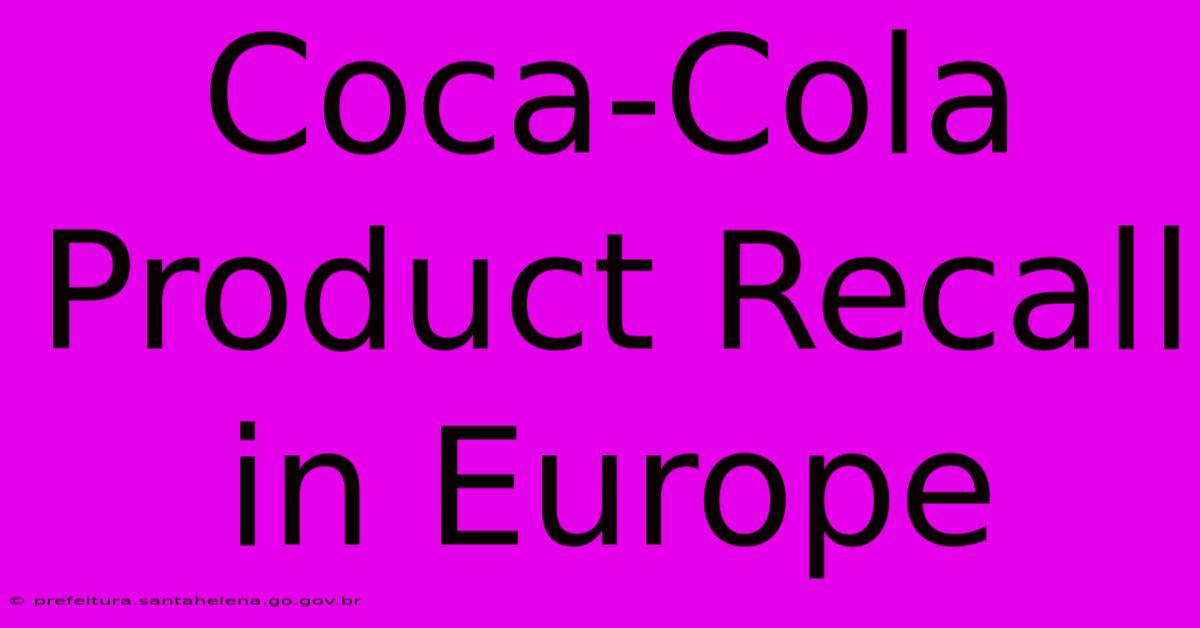
Discover more detailed and exciting information on our website. Click the link below to start your adventure: Visit Best Website. Don't miss out!
Table of Contents
Coca-Cola Product Recall in Europe: A Comprehensive Overview
Coca-Cola, a global beverage giant, enjoys immense popularity worldwide. However, its history isn't without instances of product recalls, some of which have significantly impacted the European market. While a large-scale, Europe-wide Coca-Cola recall is rare, smaller, localized incidents have occurred, prompting investigations and changes in manufacturing and distribution practices. This article delves into the history of Coca-Cola product recalls in Europe, analyzing their causes, consequences, and the company's response. We will explore the complexities of product safety regulations, consumer trust, and the challenges faced by multinational corporations in maintaining consistent quality control across vast geographical areas.
Understanding the Scope of Coca-Cola's European Operations
Before examining specific recalls, it's crucial to understand the scale of Coca-Cola's operations in Europe. The company operates numerous bottling plants and distribution networks across the continent, catering to diverse tastes and regulatory environments. This decentralized structure, while efficient for reaching a wide market, also presents challenges in ensuring uniform product quality and rapid response to potential problems. Differences in local regulations, ingredient sourcing, and manufacturing processes can contribute to localized issues that might not necessarily affect other regions.
Examining Past Instances: Localized Recalls and Their Impact
While a massive, continent-wide Coca-Cola recall hasn't occurred in recent memory, several smaller-scale incidents highlight the importance of robust quality control and swift action. These incidents, often localized to specific countries or even regions within a country, have primarily involved issues with:
-
Contamination: This is perhaps the most concerning issue, ranging from potential bacterial contamination to the presence of foreign objects in bottles. The consequences of contamination can be severe, leading to illness and significant damage to the brand's reputation. Any instances of contamination, no matter how small the scale, are treated with utmost seriousness due to the potential for widespread health concerns.
-
Packaging Defects: Problems with bottling or packaging can lead to recalls. This might involve faulty seals, damaged containers, or incorrect labeling. While less serious than contamination, these issues still affect consumer confidence and necessitate corrective actions. The company's response to these issues is crucial in minimizing negative press and regaining consumer trust.
-
Ingredient Issues: Occasionally, problems with the sourcing or processing of ingredients can necessitate a recall. This might involve the detection of contaminants in a specific batch of an ingredient used in Coca-Cola products. Stringent quality checks at all stages of the supply chain are vital to prevent such occurrences.
-
Mislabeling or Incorrect Information: While not directly related to product safety, inaccuracies in labeling or promotional materials can also lead to recalls or corrections. Transparency and accurate communication are paramount to maintaining consumer trust.
Coca-Cola's Response Mechanism: A Case Study Approach
Coca-Cola's response to any product quality concern, regardless of scale, generally follows a consistent pattern:
-
Immediate Investigation: Upon receiving reports of a potential problem, the company initiates a thorough investigation to determine the root cause. This involves tracing the product's origin, examining manufacturing processes, and testing samples.
-
Swift Action: If a problem is confirmed, Coca-Cola acts quickly to remove the affected products from the market. This involves coordinating with distributors and retailers to recall the affected batches.
-
Transparent Communication: The company emphasizes transparent communication with consumers, regulatory bodies, and stakeholders. This involves providing clear information about the recall, the affected products, and the steps being taken to address the issue.
-
Corrective Actions: Coca-Cola implements corrective actions to prevent similar incidents from happening again. This might involve changes in manufacturing processes, improved quality control measures, or adjustments to the supply chain.
-
Consumer Compensation (where applicable): In cases where consumers have experienced illness or other harm due to a defective product, Coca-Cola generally offers appropriate compensation.
The Importance of Regulatory Compliance and Consumer Trust
Navigating the complexities of European food safety regulations is paramount for Coca-Cola. Each country within the EU, and indeed across Europe, has its own specific regulations and standards. Coca-Cola must ensure that its products comply with all relevant regulations to avoid legal repercussions and maintain consumer trust. Consumer trust is a valuable asset, and any recall, regardless of size, can negatively impact brand perception. Therefore, proactive measures and transparent communication are crucial to mitigate the damage.
Lessons Learned and Future Implications
The instances of localized recalls in Europe offer valuable lessons for Coca-Cola and other multinational corporations. These experiences underscore the importance of:
-
Robust Quality Control Systems: Implementing rigorous quality control measures at every stage of the production process, from ingredient sourcing to final packaging, is crucial to preventing product defects.
-
Effective Traceability Systems: The ability to quickly trace the origin and distribution of a product is vital in the event of a recall. Advanced traceability systems can significantly speed up the recall process and minimize disruption.
-
Proactive Risk Management: Regular audits, risk assessments, and proactive monitoring of the supply chain can help identify potential problems before they escalate.
-
Strong Communication Strategies: Open and honest communication with consumers, regulators, and stakeholders is essential in building and maintaining trust during a recall situation.
In conclusion, while large-scale Coca-Cola product recalls in Europe are uncommon, localized incidents highlight the complexities of managing a global brand. The company's response mechanisms, emphasizing swift action, transparency, and corrective measures, are crucial in mitigating the impact of such events. Continuous improvement in quality control, traceability, and risk management are essential to safeguarding consumer safety and maintaining the company's reputation in the European market. The future of Coca-Cola's European operations hinges on its ability to maintain these high standards and adapt to evolving regulations and consumer expectations.
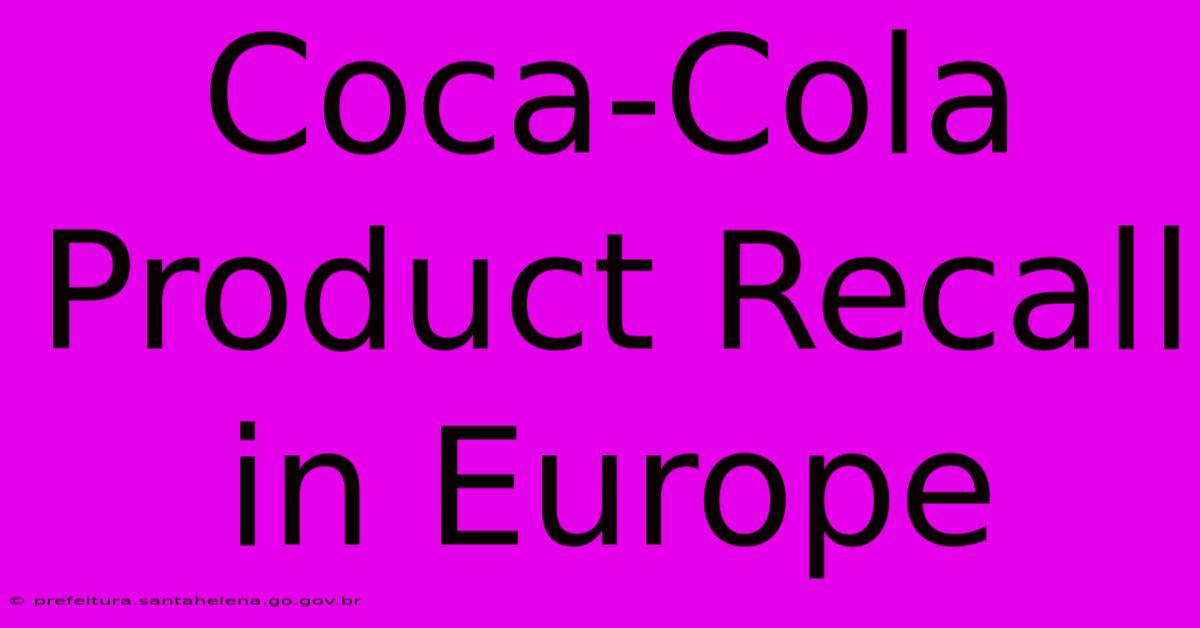
Thank you for visiting our website wich cover about Coca-Cola Product Recall In Europe. We hope the information provided has been useful to you. Feel free to contact us if you have any questions or need further assistance. See you next time and dont miss to bookmark.
Also read the following articles
Article Title | Date |
---|---|
Neymar Back In Brazil Santos Finalizes Signing | Jan 28, 2025 |
Neymars New Club Santos Officially Announces | Jan 28, 2025 |
Popular Burger Restaurant To Close | Jan 28, 2025 |
Jazzs Defensive Issues Loss Against Bucks | Jan 28, 2025 |
European Coca Cola Recall Announced | Jan 28, 2025 |
Official Threatens Gomez Deportation | Jan 28, 2025 |
Al Hilal Neymar Split Confirmed | Jan 28, 2025 |
Davos Club Politico Argentino Repudia A Milei | Jan 28, 2025 |
Uruguay 6 0 Paraguay Sudamericano Sub 20 | Jan 28, 2025 |
Raptors Defense Key In Pelican Victory | Jan 28, 2025 |