Coca-Cola Recall: European Contamination
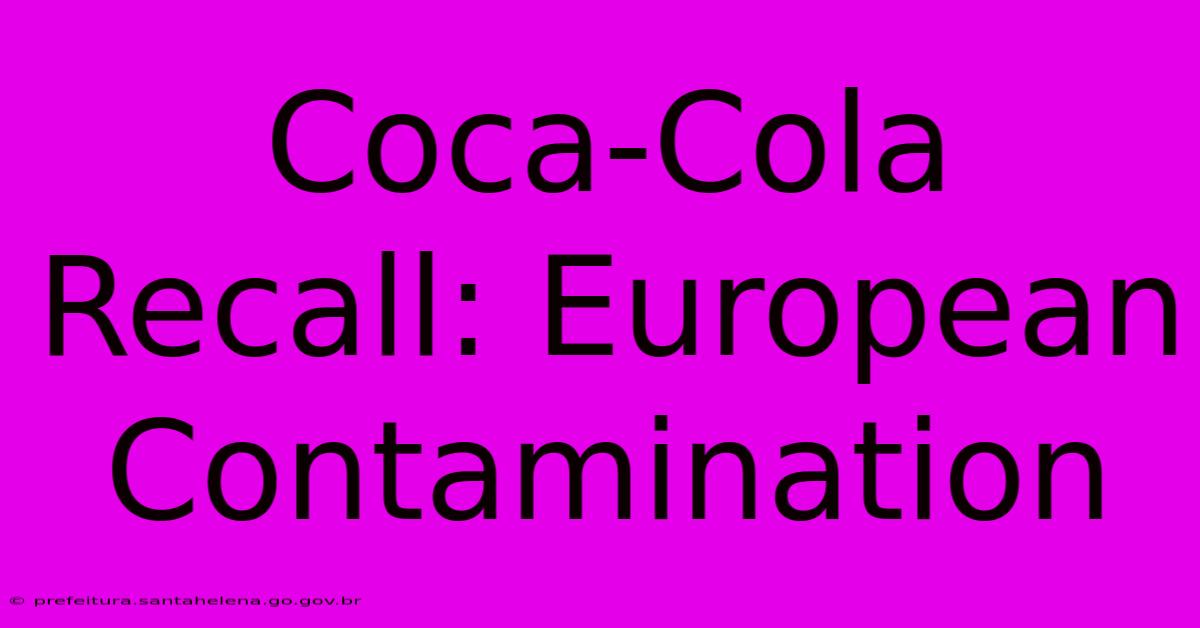
Discover more detailed and exciting information on our website. Click the link below to start your adventure: Visit Best Website. Don't miss out!
Table of Contents
Coca-Cola Recall: A European Contamination Crisis
The Coca-Cola brand, a global behemoth synonymous with refreshment, has, throughout its history, faced various challenges. However, few events have tested its resilience like the recurring scares surrounding product contamination, particularly those affecting European markets. While not every incident results in a widespread recall, the potential for such a crisis looms large, demanding stringent quality control and rapid response mechanisms. This article delves into the complexities of Coca-Cola recalls stemming from European contamination, exploring the causes, consequences, and the brand's strategies for damage control.
Understanding the Stakes: Why European Contamination Matters
Europe represents a significant market for Coca-Cola, with diverse consumer preferences and stringent regulatory frameworks. Any contamination incident, regardless of scale, can have far-reaching consequences:
-
Brand Reputation Damage: Coca-Cola's reputation for quality and safety is paramount. A contamination incident can severely tarnish this image, leading to decreased consumer trust and sales. The long-term impact can be substantial, requiring extensive rebuilding efforts.
-
Financial Losses: Recalls are enormously expensive, encompassing costs associated with product retrieval, disposal, investigations, public relations, and potential legal battles. The financial fallout extends beyond immediate costs, impacting shareholder value and future investments.
-
Regulatory Scrutiny: European regulatory bodies are highly vigilant in protecting consumer health and safety. A contamination incident can trigger intensive investigations, potential fines, and stricter regulations, increasing compliance costs for the company.
-
Consumer Health Concerns: The primary concern, naturally, is consumer safety. Contamination, depending on its nature and extent, can lead to serious health consequences, ranging from mild discomfort to severe illness, potentially resulting in legal action against the company.
Types of Contamination and Their Sources
Contamination incidents associated with Coca-Cola products in Europe have varied in nature and source:
-
Microbial Contamination: This is a significant concern, encompassing bacteria, mold, and other microorganisms that can cause illness. Sources can include contaminated water, inadequate sanitation at production facilities, or improper handling during distribution.
-
Chemical Contamination: This could involve the presence of harmful chemicals, either accidentally introduced during the manufacturing process or due to contamination of ingredients. This might stem from issues with suppliers, faulty equipment, or improper storage.
-
Foreign Object Contamination: This involves the presence of foreign objects in the final product, such as glass shards, metal pieces, or insects. This typically arises from issues in the manufacturing process or inadequate quality control checkpoints.
Case Studies: Examining Past Incidents
While specific details of Coca-Cola recalls are often kept confidential due to commercial sensitivity and ongoing legal proceedings, analyzing past reported instances helps understand the challenges:
-
The "Mystery Illness" Cases: Several isolated incidents have involved reports of consumers experiencing unexplained illnesses after consuming Coca-Cola products. Although not always directly linked to contamination, these instances highlight the importance of rigorous investigation and transparent communication.
-
Supplier-Related Contamination: Concerns have arisen in the past surrounding the quality of ingredients supplied to Coca-Cola's European bottling plants. Ensuring the highest standards from suppliers is crucial for preventing contamination at the source.
-
Packaging Defects: Cases of damaged or compromised packaging have occasionally been reported, leading to concerns about potential contamination. Robust quality control measures throughout the supply chain, from production to distribution, are essential to mitigate such risks.
Coca-Cola's Response Mechanisms: Damage Control and Prevention
Coca-Cola's response to potential contamination incidents typically involves several key steps:
-
Rapid Product Retrieval: Immediate removal of potentially affected products from the market is crucial to minimizing harm and preventing further spread. This requires efficient supply chain management and close cooperation with retailers.
-
Thorough Investigation: A comprehensive investigation is undertaken to identify the source and nature of the contamination. This often involves collaborations with regulatory bodies, independent laboratories, and internal quality control teams.
-
Transparent Communication: Open and honest communication with consumers, regulatory bodies, and the media is vital for maintaining trust and managing public perception. Transparency helps mitigate negative publicity and demonstrates accountability.
-
Preventive Measures: Following an incident, Coca-Cola typically implements enhanced preventive measures, including improved quality control protocols, enhanced sanitation procedures, and stricter supplier audits. This aims to prevent future occurrences and bolster consumer confidence.
The Future of Coca-Cola's European Operations: Lessons Learned
The European market's stringent regulations and consumer awareness necessitate continuous vigilance from Coca-Cola. Future success hinges on:
-
Investing in Technology: Advanced technologies, such as improved detection systems and automated quality control processes, can significantly enhance product safety and minimize risks.
-
Strengthening Supplier Relationships: Close collaborations with suppliers, including stringent quality audits and shared responsibility for safety, are vital for preventing contamination at the source.
-
Proactive Risk Management: Moving beyond reactive responses to contamination incidents requires proactive risk assessment and mitigation strategies. This involves continuous monitoring of potential hazards and implementing preventative measures before incidents occur.
-
Consumer Engagement: Building and maintaining strong relationships with consumers through transparent communication and active engagement in addressing concerns is crucial for building trust and loyalty.
In conclusion, while Coca-Cola's European operations have faced challenges related to product contamination, the company's ability to manage these crises effectively will determine its long-term success. A combination of stringent quality control, transparent communication, and continuous improvement will be crucial in maintaining consumer confidence and upholding the brand's reputation in this vital market. The long-term impact of any contamination scare is significant, underlining the importance of proactive measures and a commitment to product safety as the cornerstone of the business.
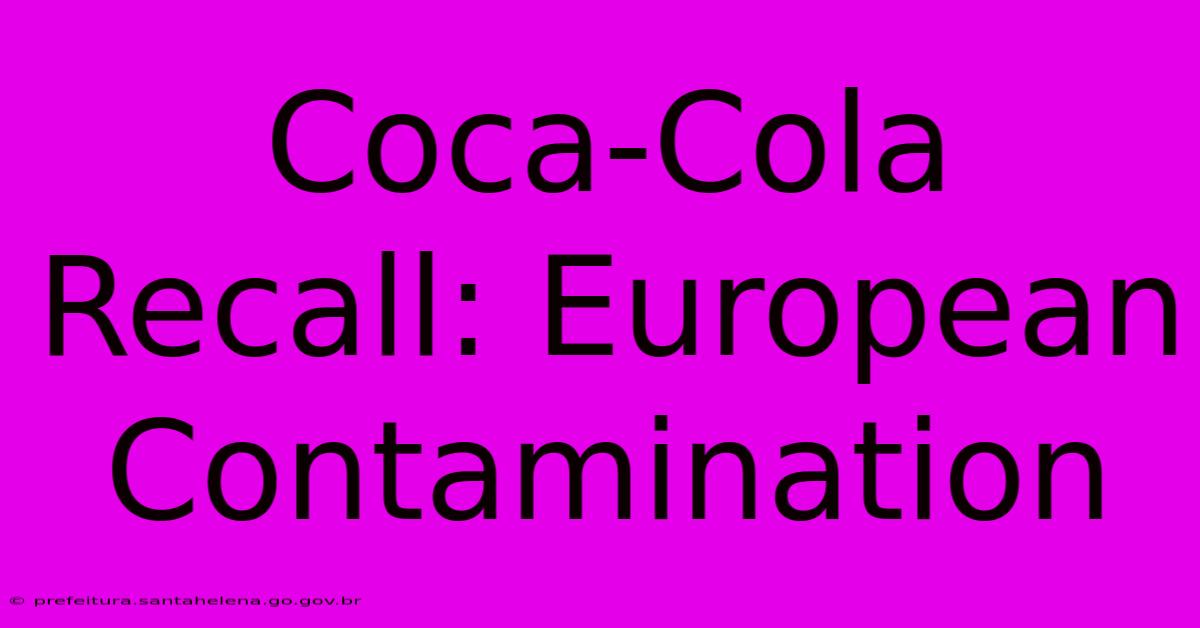
Thank you for visiting our website wich cover about Coca-Cola Recall: European Contamination. We hope the information provided has been useful to you. Feel free to contact us if you have any questions or need further assistance. See you next time and dont miss to bookmark.
Also read the following articles
Article Title | Date |
---|---|
Milwaukee Edges Out Utah Jazz | Jan 28, 2025 |
Triunfo De Uruguay 6 0 Ante Paraguay Sub 20 | Jan 28, 2025 |
El Club Politico Argentino Y El Rechazo A Milei | Jan 28, 2025 |
Jan 28 Nba Bucks Win Over Jazz 125 110 | Jan 28, 2025 |
Partido Uruguay Paraguay Ver En Vivo | Jan 28, 2025 |
Ist Die Nvidia Aktie Zu Unrecht Gefallen | Jan 28, 2025 |
Nvidia Aktiencrash Der Trump Deep Seek Effekt | Jan 28, 2025 |
Detroit Signs Forward Dominik Shine | Jan 28, 2025 |
Selena Gomez Cries Over Trumps Actions | Jan 28, 2025 |
Referee Coote Opens Up On Sexuality | Jan 28, 2025 |