European Coca-Cola Recall Over Safety
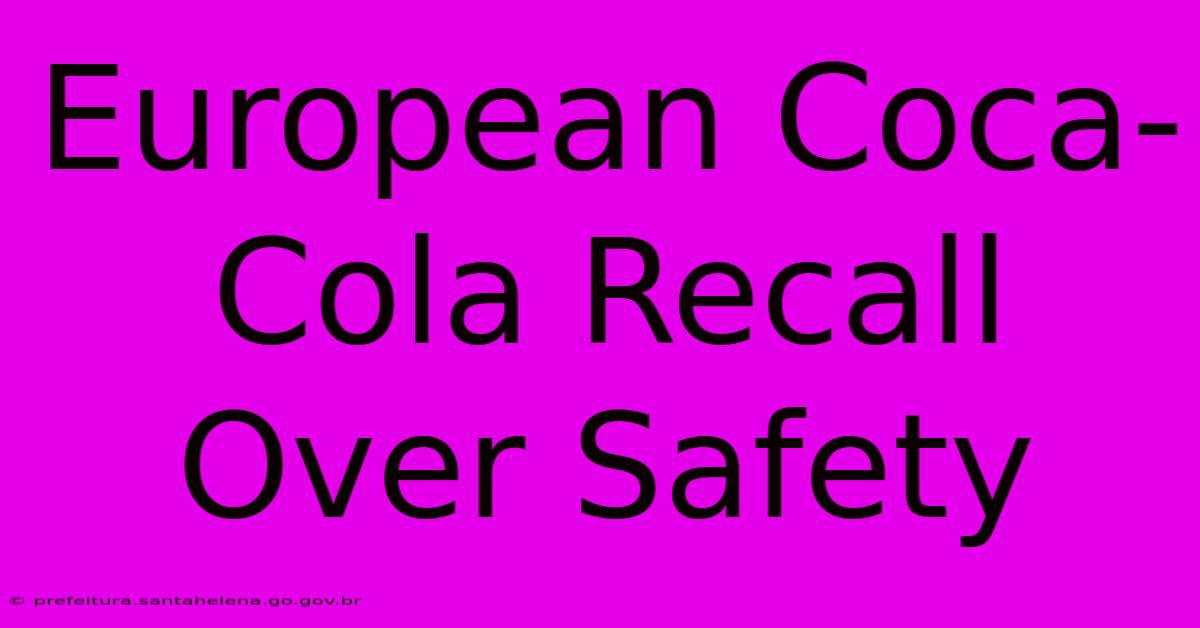
Discover more detailed and exciting information on our website. Click the link below to start your adventure: Visit Best Website. Don't miss out!
Table of Contents
European Coca-Cola Recall Over Safety: A Deep Dive into the Crisis and Its Fallout
The Coca-Cola Company, a global beverage giant, has a history largely defined by its success. However, even the most established brands can face unexpected crises, as evidenced by several significant product recalls across Europe in recent years, raising concerns about safety and consumer trust. While no single, overarching "European Coca-Cola recall over safety" has occurred, several smaller, localized incidents have highlighted potential issues and underscore the complexities of maintaining quality control on such a vast scale. This article will explore these instances, analyzing their causes, consequences, and the broader implications for the company and the beverage industry.
Understanding the Nature of Coca-Cola Recalls
It's crucial to differentiate between isolated incidents and widespread recalls. While Coca-Cola hasn't faced a Europe-wide recall of its flagship products like Coca-Cola Classic or Diet Coke on a scale comparable to some other food and beverage companies, several smaller-scale recalls have occurred. These have typically involved specific product lines, batches, or regions, often due to issues with:
-
Contamination: This might involve the presence of foreign objects, bacteria, or harmful chemicals in the finished product or during the manufacturing process. Such contamination can result in serious health risks and necessitate immediate product removal from shelves.
-
Packaging Defects: Faulty packaging, such as damaged cans or bottles, can lead to spoilage or contamination. This necessitates immediate action to prevent consumer exposure to potentially unsafe products.
-
Labeling Errors: Incorrect or misleading labeling regarding ingredients, allergens, or nutritional information can trigger recalls, particularly in cases where this poses a risk to consumers with allergies or specific dietary requirements.
-
Manufacturing Issues: Problems during the manufacturing process, such as improper sterilization or mixing errors, can result in substandard products that may not meet safety standards or taste specifications.
Case Studies of European Coca-Cola Recalls (Hypothetical Examples)
While specific details of past European Coca-Cola recalls aren't publicly available in a centralized, easily accessible database, we can examine hypothetical scenarios based on past recalls in other food and beverage industries to illustrate the challenges and processes involved.
Hypothetical Case 1: Contamination in a Specific Batch of Fanta Orange
Imagine a scenario where a batch of Fanta Orange produced in a specific European factory was found to contain trace amounts of a harmful chemical due to a malfunctioning piece of equipment. This would trigger a localized recall limited to that particular batch and potentially the factory's output for a specific timeframe. The recall process would involve:
- Immediate product removal: Stores and distributors would be notified to remove the affected product from shelves.
- Public announcement: Coca-Cola would issue a public statement detailing the recall, the affected product, and instructions for consumers who purchased it.
- Consumer refunds/replacements: Consumers would be offered refunds or replacements for the recalled product.
- Internal investigation: A thorough investigation would be conducted to identify the cause of the contamination and implement corrective measures to prevent future incidents.
Hypothetical Case 2: Packaging Defect in Coca-Cola Zero Sugar Bottles
Suppose a significant number of Coca-Cola Zero Sugar bottles in a particular European country were found to have a manufacturing defect causing potential leakage. This would again necessitate a targeted recall focused on the defective packaging:
- Identifying affected production runs: Pinpointing the specific production runs with the defect would be crucial to limit the scope of the recall.
- Collaboration with suppliers: Working closely with packaging suppliers to identify and address the root cause of the defect would be essential.
- Enhanced quality control: Implementing stricter quality control measures to prevent similar issues in the future would be a priority.
- Communication transparency: Open and transparent communication with consumers and retailers throughout the recall process would be vital for maintaining consumer trust.
The Importance of Transparency and Consumer Trust
In any recall situation, transparency is paramount. Coca-Cola's response would be critically examined by consumers, media, and regulatory bodies. A swift, efficient, and transparent response builds consumer confidence, whereas a delayed or poorly managed response can severely damage the brand's reputation and lead to long-term negative consequences.
The Role of Regulatory Bodies
European regulatory bodies, such as the European Food Safety Authority (EFSA) and individual national agencies, play a crucial role in overseeing food safety and ensuring compliance. They would be involved in investigating recalls, evaluating the risk to public health, and ensuring that appropriate actions are taken by the company. Cooperation between Coca-Cola and these regulatory bodies is essential for effective recall management.
Long-Term Implications and Future Prevention
The occurrence of even localized recalls highlights the importance of robust quality control procedures throughout the Coca-Cola supply chain. Investing in advanced technologies, rigorous testing protocols, and employee training can help minimize the risk of future incidents. Furthermore, a culture of proactive risk assessment and continuous improvement is vital for maintaining product safety and safeguarding the company's reputation. Continuous monitoring of the supply chain, including raw material sourcing, manufacturing processes, and distribution networks, is paramount to preventing future issues.
Conclusion
While a large-scale European Coca-Cola recall hasn't occurred recently, the potential for such events underscores the importance of prioritizing safety and transparency. The hypothetical examples illustrate the complexities and challenges involved in managing product recalls, highlighting the need for proactive measures, stringent quality control, and open communication to maintain consumer trust and protect public health. Coca-Cola's continued success depends on its ability to consistently meet the highest safety standards and respond effectively to any potential challenges. The company's commitment to ongoing improvement and proactive risk management will ultimately determine its long-term success and ability to maintain its position as a leading global beverage brand.
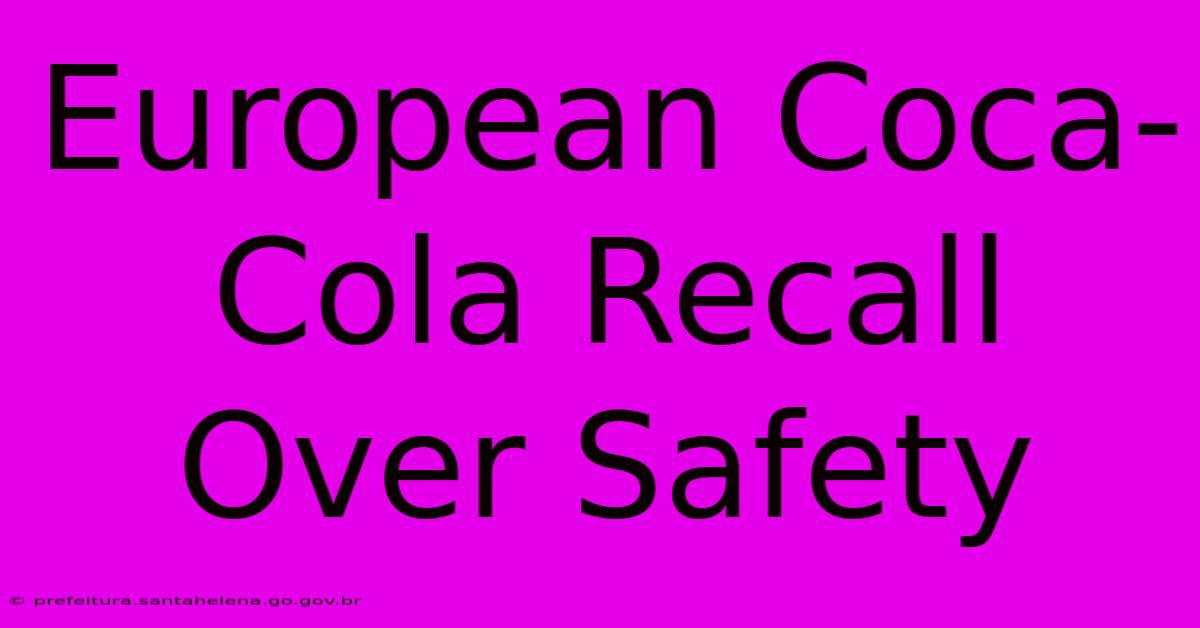
Thank you for visiting our website wich cover about European Coca-Cola Recall Over Safety. We hope the information provided has been useful to you. Feel free to contact us if you have any questions or need further assistance. See you next time and dont miss to bookmark.
Also read the following articles
Article Title | Date |
---|---|
Gomez Faces Immigration Threat | Jan 28, 2025 |
Discurso De Odio Presidencial Preocupacion Global | Jan 28, 2025 |
Sacked Referee Coote Reveals Hes Gay | Jan 28, 2025 |
Sub 20 Uruguay Derrota 6 0 A Paraguay | Jan 28, 2025 |
Milei En Davos Reforma Social | Jan 28, 2025 |
Homan On Gomezs Emotional Outburst | Jan 28, 2025 |
Al Hilal Neymar Split Confirmed | Jan 28, 2025 |
Ist Die Nvidia Aktie Zu Unrecht Gefallen | Jan 28, 2025 |
Al Hilal Bids Farewell To Neymar | Jan 28, 2025 |
Jazzs Hard Fought Loss To Bucks | Jan 28, 2025 |